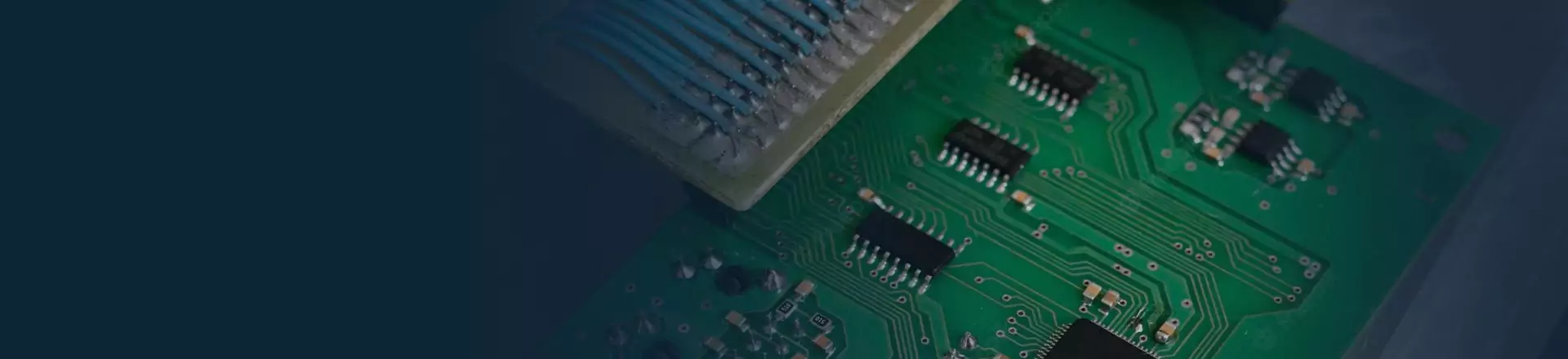
Rigid-Flex PCB Manufacturer
A rigid-flex printed circuit board (PCB) is a type of PCB that combines the advantages of both rigid and flexible PCBs. It is made up of a combination of rigid and flexible layers, which allows it to be both rigid and flexible in different areas.
Rigid-Flex PCB Manufacturing Solutions
Rigid flex printed circuit boards are boards that use a combination of flexible and rigid board technologies. Most rigid flex boards consist of multiple layers of flexible circuit substrates attached to one or more rigid boards externally and/or internally, depending upon the design of the application.There are several benefits to using rigid-flex PCBs. They are more durable than traditional flexible PCBs because they have a rigid layer, which helps to protect the flexible layer. They also have a higher density of components, which allows for more complex circuits to be designed. In addition, rigid-flex PCBs can be used in applications where space is limited, as they can be bent or folded to fit into tight spaces.
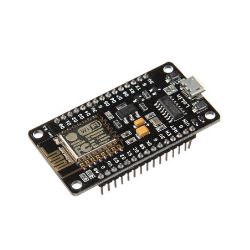
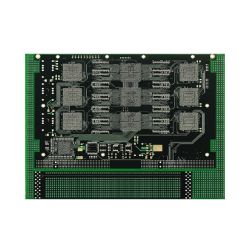
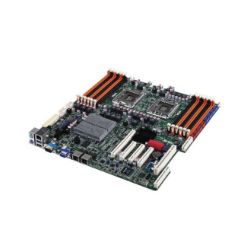
We can provide to...
- Turn times as short as 24 hours
- 1 to 100,000 units
- Class II Inspection standard and Class III Inspection available
- 100% on-time guarantee
- DFM support
- Lead free (RoHS) options
- SMT and thru-hole capabilities
- All SMT machine placed
- AOI (Automated Optical Inspection)
- Lead-free RoHS Certification and ITAR compliance screen available
-
Program Design
-
flex Board Capability
-
PCB manufacturing Capabilities
-
Equipment Exhibition
From component purchasing to function test and package finish , we provide one shop stop services for every types of PCB.
flex Board Capability
Layer Count | 1-6L 1-4 L normal |
Board Thickness | 0.1-0.5mm (1-4L) 0.6-0.8mm (5-6L) |
The tolerance of 1L board thickness | ±0.03mm |
The tolerance of 2L board thickness | ±0.03mm |
The tolerance of multilayer board thickness | ±10% (Normal ±0.1mm) |
The tolerance of multilayer board thickness | ±10% (Normal ±0.05mm) |
The tolerance of board thickness | ±10% (Normal ±0.1mm) |
The tolerance of board thickness | 9inch*23inch(PI≥1mil) 9inch*14inch (normal) |
Max finished board size | 2mm*4mm(no connection tab);8mm*8mm(with connection tab) |
Min finished board size | 生益 SF305: PI=0.5mil, 1mil, 2mil; Cu=0.33OZ, 0.5OZ, 1OZ |
Adhesive flex core | 杜邦AP:PI=1mil,2mil,3mil,4mil;Cu=0.5oz,1oz, 2oz |
Adhesiveless core | 杜邦AP:PI=1mil,2mil,3mil,4mil;Cu=0.5oz,1oz, 2oz |
Thermosetting adhesive | 杜邦LF:0110,0210 |
PI stiffener | 台虹 MHK 系列: PI=3mil, 5mil , 7mil, 9mil |
3M tape | 9077,9460 |
Finished copper thickness 12um / 18um | 3/3mil |
Finished copper thickness 35um | 4/3.5mil |
Finished copper thickness 70um | 6/5mil |
Solder mask bridge min. (copper thickness<=1oz) | 4mil(Green),5mil(White),8.0mil(big copper area) |
Solder mask opening (single side) | 6mil,8mil(big copper area) |
Solder mask opening of NPTH (single side) | 3mil(partial2.5mil) |
Min. coverlay bridge | 8mil |
Finished copper thickness 12um / 18um | 5/5mil (after compensation) |
Finished copper thickness 35um | 6.5/5mil (after compensation) |
Finished copper thickness 70um | 10/8mil (after compensation) |
Min. Inner layer annual ring width | 4mil(<4L),7mil(4-6L),9mil(7-8L) |
The min distance between inner layer isolated pad and copper area | 3.5mil 4mil normal |
Max finished inner layer copper thickness | 3oz 2 oz normal |
Finished copper thickness, before compensation | 3/3mil |
Finished copper thickness 35um, before compensation | 3.5/3.5mil |
Finished copper thickness 70um, before compensation | 5.5/5mil |
Finished copper thickness 35um, | 3mil(<2mm);4mil(2-4.5mm) |
Finished copper thickness 35-70um, | 5mil(<2mm);6mil(2-4.5mm) |
Finished copper thickness >70um, | 7mil(<2mm);10mil(2-4.5mm) |
Min the distance between NPTH edge to external conductor before compensation | 4oz 2 oz normal |
Max finished external copper thickness | 8mil 5mil(Gold finger area) |
The max board thickness for 0.15mm drill bit | 0.8mm |
Min laser hole diameter | 0.1mm |
Min finish half PTH via diameter | 0.3mm |
Min NPTH tolerance | ±2mil(limit+0,-2mil or +2mil,-0) |
Min space between via hole walls in different net, before compensation | 10mil(after compensation) 12mil (normal)(after compensation) |
Tolerance of stiffener tape | ±0.1mm (Normal ±0.2mm) |
Tolerance of Coverlay | ±2mil ((Normal ±4mil) |
Min distance between coverlay opening and conduct | 3mil ((Normal 4mil) |
PCB manufacturing Capabilities
Normal Tg FR4(Halogen free) | Shengyi S1150 |
High Tg FR4(Halogen free) | Shengyi S1165 |
HDI PCB material | LDPP(IT-180A 1037,1086)、Normal 106,1080 |
High Tg FR4 | Isola:FR408、FR408HR、IS410、FR406、GETEK、PCL-370HR |
Ceramic Particle Filled Laminates | Rogers:Rogers4350、Rogers4003;Arlon:25FR、25N; |
PTFE Laminates | Rogers、Taconic、Arlon、Nelco、TP |
PTFE PP | Taconic:TP、TPN、HT1.5(1.5mil)、Fastrise |
Rigid PCB | Back board、HDI、 |
Blind&buried via type | Laminating≤3 times |
HDI PCB | 1+n+1、1+1+n+1+1、2+n+2、3+n+3 |
Lead free | Flash gold、ENIG |
aspect ratio | 10:01:00 |
Max finished size | HAL Leaded 22"*39" |
MIN finished size | HAL Leaded 5"*6" |
PCB thickness | HAL Leaded0.6-4.0mm; |
MAX high to gold finger | 1.5inch |
Min space between gold fingers | 6mil |
Min block space to gold fingers | 7.5mi |
Max lamination cycle | 3 times |
Min laser drill for stacked via | 0.1mm |
Min stacked via pad size | 0.3mm |
Max laser drilling size | 0.15mm |
Blind Via Finished Hole Size | 0.3mm |
Buried Via Finished Hole Size | 0.3mm |
Non Conductive Filled Vias | 0.2mm~0.8mm |
Conductive Filled Vias | 0.2~0.8mm |
ENIG (Electroless Nickel/Immersion Gold) | AU: 0.05~0.1um Nickel: 3~5um |
Hard gold | 0.1~1.0um |
Soft gold | 0.1~1.0um |
Lead Free HASL | 2~40um |
Flash gold(electroplated gold) | Au 0.025-0.10um,Nickel 3~5um |
electroplated Gold finger | Au 0.25-1.0um Nickel 3~5um |
Selective Gold | Au 0.25-1.0um Nickel 3~5um |
Tin Nickel | N/A |
Immersion Silver | 0.2~0.4um |
Soldermask | min. 8um, max. 30um |
Min mechanical hole 4mil/6mil/8mi | 0.8mm/1.5mm/2.5mm |
Finshed mechanical hole size | 0.1~6.0mm |
MAX aspect ratio for Hole | 12:01:00 |
Max aspect ratio for mechanical depth- control | 1.3:1 |
Min. depth of Mechanical depth- control(backdrill) | 0.2mm |
Min gap between hole wall conductor | 7mil |
Min space between laser holes and conductor | 5mil |
Min space bwteen hole walls in different net | 12mil |
Min space bwteen hole walls in same net | 8mil |
Min space bwteen NPTH hole walls | 10mil |
Hole location tolerance | '+/-3mil |
NPTH tolerance | '+/-0.05mm |
Pressfit holes tolerance | '+/-0.05mm |
Countersink depth tolerance | '+/-0.15mm |
Countersink hole size tolerance | '+/-0.15mm |
Min Pad size for laser drillings | 0.25mm |
Min Pad size for mechanical drilling | 0.4mm |
Min Pad size for mechanical drilling | 0.3mm |
Min BGA pad size | 0.4mm |
Pad size tolerance(BGA) | '+/-2mil |
Min lead pitch | 0.3mm |
Min BGA ball pitch | 0.3mm |
Internal Layer | 1/3OZ: N/A |
Internal Layer | 1/2OZ: 3.5/3.5mil |
Internal Layer | 1OZ: 3/4mil |
Internal Layer | 2OZ: 4/5mil |
External Layer | 1/3OZ: 3/3mil |
External Layer | 1/2OZ:3.5/3.5mil |
Width tolerance | ≤10mil:+/-20% |
Min copper pour to Pour | 7mil |
Min copper pour to trace | 4mil |
Min copper pour to microvia | 8mil |
Min copper pour to buired via | 4mil |
Min copper pour to SMD Pad | 5mil |
Min copper pour to PTH Pad | 5mil |
Soldermask color | Semi Gloss greeen\Gloss Green\Matte Green\Black\Red\Blue\Yellow |
Solder Mask Min Dam Size | 4mil |
Solder Mask Min Dam Size in BGA Area | 4mil |
Solder Mask Registration | '+/-4mil |
Silkscreen color | White, yellow , black |
Min width of soldermask bridge | White, yellow , black |
Min width of soldermask bridge | 4mil |
Min. Diameter Rout Cutter Available | 0.6mm |
Routed Part Size Tolerance | '+/-0.15mm |
V-CUT symmetrical tolerance | '+/-0.1mm |
MAX V-CUT lines | 80 lines |
V-CUT angle tolerance | '+/-5 degress |
V Score, Edge to Copper | H≤1.0mm:0.3mm(20°)、0.33mm(30°)、0.37mm(45°); |
V Score, Edge to Copper | 1.0<H≤1.6mm:0.36mm(20°)、0.4mm(30°)、0.5mm(45°); |
V Score, Edge to Copper | 1.6<H≤2.4mm:0.42mm(20°)、0.51mm(30°)、0.64mm(45°); |
V-CUT angle | 20、30、45 degree |
Gold finger bevelling | 20、30、45、60 degree |
Gold finger bevelling tolerance | '+/-5 degree |
Min space of gold finger chamfering | 6mm |
Min gap between the side of | 8mil |
Layer count | 1~28 layer |
PCB thickness | 0.4~6..0mm |
PCB thickness tolerance˄Normal | Thickness : ±10%(>1.0mm);±0.1mm(≤1.0mm); |
PCB thickness tolerance˄Special ˅ | Thickness ±0.1mm(≤2.0mm);±0.15mm(2.1-3.0mm) |
Min bow&twist | 0.75% |
Controlled Impedance Tolerance | '+/-10% |
Testing methods | Flying probe testing, Test fixture |
Quality standards | IPC II, IPC III |
PCB Products show
Testing Procedures
There are many rigid-flex PCB manufacturers available, and the best one for you will depend on your specific needs and requirements. Some factors to consider when choosing a manufacturer include the type of materials used, the quality of the manufacturing process, and the cost of the PCBs. It may also be helpful to look for a manufacturer that has experience in producing PCBs for your industry or application.
To find a rigid-flex PCB manufacturer, you can do an online search and compare quotes from different companies. You can also ask for recommendations from other professionals in your industry or reach out to industry associations or trade organizations for suggestions. It is always a good idea to do your research and ask for references before choosing a manufacturer to ensure that you are getting a high-quality product.
Overall, rigid-flex PCBs offer a number of benefits for applications that require flexibility, durability, and a compact design. They are an important tool in the design and manufacturing of a wide range of electronic devices and systems.
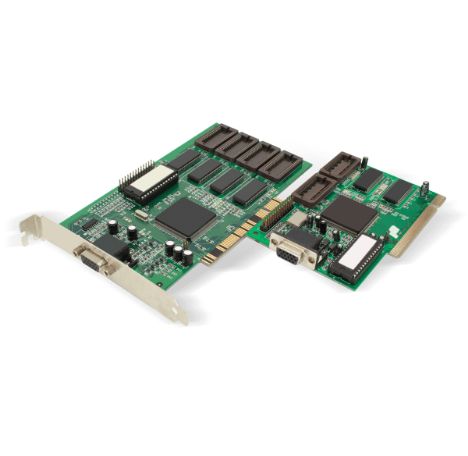
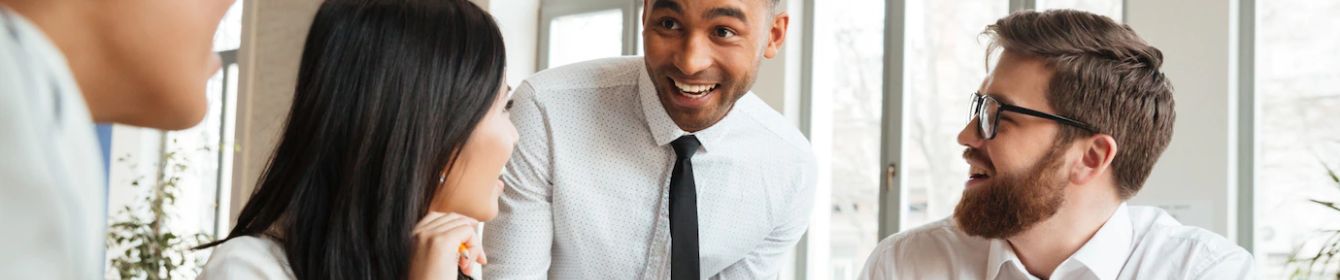
Bring you better PCB products
Circuit Board Fabrication and PCB Assembly Turnkey Services
Rigid-Flex PCB asked questions
What is a rigid-flex PCB?
What are the advantages of using a rigid-flex PCB?
How is a rigid-flex PCB made?
Are rigid-flex PCBs more expensive than traditional PCBs?
Can a rigid-flex PCB be used in place of a traditional PCB?
Why Choose Us?
Since 2018, WINOW has offered good-quality PCBs with excellent turnaround times and customer satisfaction. We are one of the biggest and most skilled board manufacturers in China.
-
Prototype orders placed within 24 hours
-
Normal lead time (5-7 Working days for some PCBs prototypes and small batch production)
-
Faster lead time (48 hours for some PCBs prototypes and small batch production)